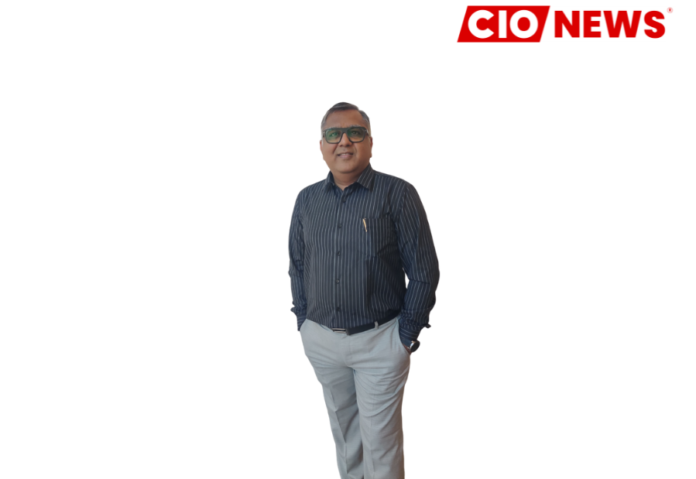
AI and machine learning will be increasingly used for predictive maintenance, quality control, and cybersecurity.
This is an exclusive article series conducted by the Editor Team of CIO News with Rajesh Shah, Chief Information officer, Nirmal Polyplast Pvt. Ltd.
In the current age, cybersecurity is crucial for manufacturing companies due to several key reasons:
Protection Against Cyber Attacks: Manufacturing companies are increasingly targeted by cybercriminals due to their reliance on interconnected systems and valuable data. Cyberattacks can disrupt production, steal intellectual property, and cause significant financial losses.
Safeguarding Operation: The integration of IT and operation in manufacturing has created new vulnerabilities. Protecting operations systems, such as industrial control systems (ICS) and supervisory control and data acquisition (SCADA) systems, is essential to prevent disruptions in production.
Ensuring Business Continuity: Cybersecurity measures help ensure that manufacturing operations can continue smoothly without interruptions caused by cyber This is vital for maintaining productivity and meeting customer demands.
Protecting Intellectual Property: Manufacturing companies often possess valuable intellectual property, including proprietary designs and processes, and cybersecurity helps protect this sensitive information from theft and unauthorized access.
Compliance with Regulations: Many industries have specific cybersecurity regulations and standards that manufacturing companies must comply with. Adhering to these regulations helps avoid legal penalties and enhances the company’s reputation.
Mitigating Supply Chain Risks: Manufacturing companies are part of complex supply chains. Security measures help protect not only the company but also its suppliers and partners, reducing the risk of supply chain disruptions.
o Adapting to Technological Advancements: The adoption of technologies like the Internet of Things (IoT), artificial intelligence (AI), and cloud computing in manufacturing has increased the attack surface. Robust cybersecurity measures are needed to protect these advanced systems.
In summary, cybersecurity is essential for manufacturing companies to protect their operations, data, and intellectual property, ensure business continuity, comply with regulations, and mitigate supply chain risks. By investing in cybersecurity, manufacturers can safeguard their assets and maintain a competitive edge in the market.
Manufacturing companies face several common vulnerabilities and threats that can be exploited by cyber attackers. Here are some of the key ones.
- Industrial Control Systems (ICS) Vulnerabilities:
Supervisory Control and Data Acquisition (SCADA) Systems: SCADA systems are critical for managing industrial processes. Weaknesses in these systems can lead to unauthorized access and control.
o Electric Devices: Devices such as power analyzers and relay platform units can have vulnerabilities that attackers exploit to disrupt operations.
- Unpatched Software and Firmware:
o Outdated Systems: Many manufacturing systems run on outdated software and firmware, which may have known vulnerabilities that have not been patched.
Third-Party Components: Vulnerabilities in third-party software and hardware components can also pose significant risks.
- Weak authentication and access controls:
Poor Password Policies: Weak or default passwords can be easily exploited by attackers to gain access to critical systems.
Lack of Multi-Factor Authentication (MFA): Not implementing MFA can make it easier for attackers to breach systems using stolen credentials.
Using default credentials in manufacturing environments poses several significant risks:
Unauthorized Access: Default credentials are often well-known and easily accessible through product documentation or online sources. Attackers can exploit these to gain unauthorized access to critical systems.
Data Breaches: Once inside the system, attackers can steal sensitive data, including intellectual property, production data, and personal information of employees and customers.
Operational Disruptions: Cyber attackers can manipulate or shut down manufacturing processes, leading to production halts, equipment damage, and significant financial losses.
Ransomware Attacks: Attackers can deploy ransomware to encrypt critical data and demand a ransom for its release. This can severely disrupt operations and result in substantial financial costs.
Lateral Movement: Once inside the network, attackers can move laterally to other systems, escalating their privileges and causing further damage across the organization.
Compromise of Industrial Control Systems (ICS): Default credentials can be used to access and control ICS, leading to potential safety hazards, equipment malfunctions, and compromised product quality.
Reputation Damage: A successful cyber-attack can damage the company’s reputation, leading to loss of customer trust and potential legal consequences.
Regulatory Non-Compliance: Failing to secure systems adequately can result in non-compliance with industry regulations and standards leading to fines and legal penalties.
- Network segmentation issues:
Flat Networks: Lack of proper network segmentation can allow attackers to move laterally within the network once they gain access.
o Remote Access Vulnerabilities: Increased remote access capabilities, especially post-pandemic, have expanded the attack surface.
- Insecure Protocols and Communication:
o Unauthenticated Protocols: Using protocols that do not require authentication can expose systems to unauthorized access.
Unencrypted Communication: Transmitting data without encryption can allow attackers to intercept and manipulate sensitive information.
- Insufficient monitoring and incident response:
Lack of Real-Time Monitoring: Without real-time monitoring, it can be difficult to detect and respond to cyber threats promptly.
o Inadequate Incident Response Plans: Not having a robust incident response plan can lead to delayed and ineffective responses to cyber incidents.
Addressing these vulnerabilities requires a comprehensive approach to cybersecurity, including regular updates and patches, strong authentication measures, network segmentation, secure communication protocols, and effective monitoring and incident response strategies.
The adoption of IoT devices and increased connectivity in manufacturing processes has significantly impacted the cybersecurity landscape in the industry. Here are some keyways this transformation has influenced cybersecurity:
- Expanded Attack Surface:
Increased Entry Points: The proliferation of IoT devices means more entry points for potential cyberattacks. Each connected device can be a potential vulnerability if not properly secured.
Complex Networks: The integration of IoT devices creates complex networks that are harder to monitor and secure comprehensively.
- Enhanced Productivity and Efficiency:
Real-Time Data: IoT devices enable real-time data collection and analysis, improving operational efficiency and decision-making. However, this also means that any disruption can have immediate and widespread effects.
Automation: Increased automation through IoT can streamline processes but also introduces new risks if automated systems are compromised.
- Increased vulnerabilities:
Legacy Systems: Many manufacturing environments still use legacy systems that were not designed with cybersecurity in mind. Integrating these with modern IoT devices can create vulnerabilities.
Insecure Protocols: IoT devices often use insecure communication protocols, making them susceptible to interception and manipulation.
- Challenges in Device Management:
Diverse Devices: The variety of IoT devices, each with different security capabilities and requirements, makes it challenging to implement uniform security measures.
Firmware Updates: Ensuring that all IoT devices are regularly updated with the latest firmware and security patches is a significant challenge.
- Supply Chain Risks:
Interconnected Supply Chains: IoT devices often connect across supply chains, increasing the risk of cyber threats propagating through interconnected systems.
Third-Party Security: Ensuring that third-party vendors and suppliers maintain robust cybersecurity practices is crucial to prevent vulnerabilities from being introduced into the network.
- Regulatory and Compliance Issues:
o Evolving Standards: Keeping up with evolving cybersecurity standards and regulations for IoT devices can be challenging for manufacturers.
Data Privacy: Protecting the vast amounts of data generated by IoT devices and ensuring compliance with data privacy regulations is critical.
- Adoption of Advanced Security Measures:
AI and Machine Learning: Manufacturers are increasingly using AI and machine learning to detect and respond to cyber threats in real-time.
Network Segmentation: Implementing network segmentation to isolate IoT devices and limit the spread of potential attacks.
In summary, while IoT devices and increased connectivity have brought significant benefits to the manufacturing industry, they have also introduced new cybersecurity challenges. Addressing these challenges requires a comprehensive approach that includes robust security measures, continuous monitoring, and collaboration with industry partners.
Manufacturing companies often face greater threats from internal resources than external ones due to several key factors:
- Insider Knowledge:
Access to Sensitive Information: Employees and internal personnel have access to critical systems, proprietary data, and intellectual property. This insider knowledge can be exploited, either intentionally or unintentionally.
- Human error:
Accidental Breaches: Many internal threats arise from human error, such as misconfigurations, accidental data leaks, or falling victim to phishing attacks.
Negligence: Employees may inadvertently expose the company to risks by not following security protocols or using weak passwords.
- Malicious Insider Threats:
Disgruntled Employees: Employees who are unhappy or have malicious intent can deliberately sabotage systems, steal data, or leak sensitive information.
o Collusion with External Attackers: Insiders may collaborate with external attackers, providing them with access or information that can be used to breach the company’s defenses.
- Lack of Monitoring and Controls:
Insufficient Oversight: Internal activities are often less monitored.
compared to external threats. This lack of oversight can allow malicious activities to go unnoticed for longer periods.
Inadequate Access Controls: Poorly implemented access controls can enable unauthorized access to sensitive areas of the network.
- Complexity of Internal Systems:
Interconnected Systems: Manufacturing environments often have complex, interconnected systems that can be difficult to secure comprehensively.
Legacy Systems: Many manufacturing companies use outdated or legacy systems that are more vulnerable to attacks and harder to secure.
- Cultural and behavioural factors:
o Complacency: Employees may become complacent about security measures, especially if they believe that threats are primarily external.
Lack of Training: Insufficient cybersecurity training can leave employees unaware of best practices and how to recognize potential threats.
Addressing these internal threats requires a comprehensive approach that includes robust access controls, continuous monitoring, regular training, and fostering a security-conscious culture within the organization.
Government regulations and industry standards play a crucial role in shaping the cybersecurity practices of manufacturers. Here are some key ways they influence the industry:
- Establishing baseline security requirements:
Regulatory Frameworks: Governments establish regulatory frameworks that set minimum cybersecurity requirements for manufacturers by each sector, like chemicals, energy, critical manufacturing, defense industries, etc. These frameworks ensure that companies implement essential security measures to protect their systems and data.
o Industry Standards: Industry standards, such as ISO/IEC 27001 and the NIST Cybersecurity Framework, provide guidelines and best practices for manufacturers to follow, helping them achieve a robust cybersecurity posture.
- Ensuring Compliance and Accountability:
Compliance Mandates: Regulations mandate compliance with specific cybersecurity practices, ensuring that manufacturers adhere to established standards. Non-compliance can result in legal penalties and reputational damage.
Audits and Assessments: Regular audits and assessments are conducted to verify compliance with cybersecurity regulations and standards. These evaluations help identify gaps and areas for improvement.
- Promoting Cybersecurity Awareness and Training:
Training Requirements: Regulations often include requirements for employee training and awareness programs. This ensures that all personnel are knowledgeable about cybersecurity risks and best practices.
Awareness Campaigns: Government and industry bodies run awareness campaigns to educate manufacturers about emerging threats and the importance of cybersecurity.
- Facilitating Information Sharing and Collaboration:
Information Sharing Initiatives: Governments and industry organizations facilitate information sharing about cyber threats and vulnerabilities. This collaboration helps manufacturers stay informed and respond effectively to emerging threats.
o Public-Private Partnerships: Partnerships between government agencies and private sector companies enhance the overall cybersecurity ecosystem by pooling resources and expertise.
- Driving Innovation and Investment:
Research and Development: Government funding and incentives for cybersecurity research and development drive innovation in security technologies and solutions.
Investment in Cybersecurity: Regulations encourage manufacturers to invest in cybersecurity measures, ensuring that they allocate sufficient resources to protect their systems and data.
- Adapting to Evolving Threats:
Dynamic Regulations: Cybersecurity regulations and standards are continuously updated to address new and evolving threats. This ensures that manufacturers remain resilient against the latest cyber risks.
Incident Response and Recovery: Regulations often include requirements for incident response and recovery plans, ensuring that manufacturers can quickly and effectively respond to cyber incidents.
In summary, government regulations and industry standards provide a structured approach to cybersecurity, ensuring that manufacturers implement necessary measures, stay compliant, and remain resilient against cyber threats. By adhering to these guidelines, manufacturers can protect their operations, data, and reputation.
Manufacturers prioritize and allocate budgets for cybersecurity initiatives and investments through a structured approach that considers various factors. Here are some key steps and considerations:
- Risk Assessment:
Identify Critical Assets: Manufacturers start by identifying their most critical assets and systems that need protection. This includes intellectual property, production systems, and customer data.
Evaluate Threat Landscape: Understanding the current threat landscape and potential vulnerabilities helps prioritize areas that require immediate attention.
- Strategic Alignment:
Business Goals: Cybersecurity investments are aligned with overall business goals and objectives. This ensures that security measures support the company’s strategic direction.
Regulatory Compliance: Ensuring compliance with industry regulations and standards is a key driver for budget allocation.
- Budget Allocation:
Prioritize High-Risk Areas: Funds are allocated to address the highest-risk areas first. This includes securing critical infrastructure, implementing advanced threat detection, and protecting sensitive data.
o Layered Security Approach: Adopting a multi-layered security approach ensures comprehensive protection across different levels of the organization.
- Employee Training and Awareness:
Training Programs: Investing in regular cybersecurity training and awareness programs for employees to reduce human error and improve overall security posture.
Phishing Simulations: Conducting phishing simulations to educate employees about recognizing and responding to phishing attacks.
- Monitoring and Incident Response:
Continuous Monitoring: Implementing continuous monitoring solutions to detect and respond to threats in real-time.
Incident Response Plans: Developing and regularly updating incident response plans to ensure quick and effective responses to cyber incidents.
- Leveraging external expertise:
Managed Security Services: Partnering with managed security service providers (MSSPs) to enhance cybersecurity capabilities and manage complex security needs.
Consulting Services: Engaging cybersecurity consultants to conduct assessments, provide recommendations, and assist with implementation.
- Performance Measurement:
Metrics and KPIs: Establishing metrics and key performance indicators (KPIs) to measure the effectiveness of cybersecurity initiatives and investments.
Regular Reviews: Conducting regular reviews and audits to assess the performance of cybersecurity measures and make necessary adjustments.
Now manufacturers understand the need for cybersecurity and effectively prioritize and allocate budgets for cybersecurity initiatives, ensuring that their investments provide the most significant protection and support their overall business objectives.
The manufacturing industry is likely to face several emerging trends and challenges in cybersecurity over the next few years. Here are some key ones:
- Increased Integration of IT and OT:
Trend: The convergence of information technology (IT) and operational technology (OT) will continue to grow, leading to more interconnected systems.
Challenge: Securing these integrated environments will be complex, as traditional IT security measures may not be sufficient for OT systems.
- Rise of Advanced Persistent Threats (APTs):
Trend: APTs will become more sophisticated, targeting specific manufacturing processes and systems.
Challenge: Detecting and mitigating these threats will require advanced threat intelligence and continuous monitoring.
- Expansion of IoT and IIoT Devices:
Trend: The use of Internet of Things (IoT) and Industrial Internet of Things (IIoT) devices will increase, enhancing automation and efficiency.
Challenge: Each connected device represents a potential vulnerability, making it essential to implement robust security measures for IoT/IIoT devices.
- Supply Chain Security:
Trend: Supply chains will become more interconnected and global.
Challenge: Ensuring the security of the entire supply chain, including third-party vendors and suppliers, will be critical to preventing breaches.
- Adoption of AI and Machine Learning:
Trend: AI and machine learning will be increasingly used for predictive maintenance, quality control, and cybersecurity.
Challenge: While these technologies can enhance security, they also introduce new risks, such as adversarial attacks on AI systems.
- Regulatory Compliance:
Trend: Cybersecurity regulations and standards will continue to evolve, becoming more stringent.
Challenge: Keeping up with these changes and ensuring compliance will require ongoing investment and adaptation.
- Remote Work and Remote Access:
Trend: The trend towards remote work and remote access to manufacturing systems will persist.
Challenge: Securing remote access points and ensuring that remote work does not introduce vulnerabilities will be essential.
- Shortage of Cybersecurity Skills:
Trend: The demand for skilled cybersecurity professionals will continue to outpace supply.
Challenge: Addressing the skills gap through training, education, and collaboration with external experts will be necessary.
- Data Privacy and Protection:
Trend: The amount of data generated by manufacturing processes will increase significantly.
Challenge: Protecting this data from breaches and ensuring compliance with data privacy regulations will be a major focus.
- Cyberphysical Security:
Trend: The integration of cyber and physical systems will grow, leading to more cyber-physical threats.
Challenge: Developing comprehensive security strategies that address both cyber and physical aspects will be crucial.
By staying ahead of these trends and proactively addressing the associated challenges, manufacturing companies can enhance their cybersecurity posture and protect their operations from evolving threats.
Do Follow: CIO News LinkedIn Account | CIO News Facebook | CIO News Youtube | CIO News Twitter
About us:
CIO News is the premier platform dedicated to delivering the latest news, updates, and insights from the CIO industry. As a trusted source in the technology and IT sector, we provide a comprehensive resource for executives and professionals seeking to stay informed and ahead of the curve. With a focus on cutting-edge developments and trends, CIO News serves as your go-to destination for staying abreast of the rapidly evolving landscape of technology and IT. Founded in June 2020, CIO News has rapidly evolved with ambitious growth plans to expand globally, targeting markets in the Middle East & Africa, ASEAN, USA, and the UK.
CIO News is a proprietary of Mercadeo Multiventures Pvt Ltd.